Elevating contract manufacturing quality and throughput with zero-shot visual inspection AI
Objective
Improve contract manufacturing quality and throughput to increase profitability
Technology
AI for visual inspection
+ Defect detection +
Zero-shot learning
Industry
Manufacturing + Contract manufacturing + industrial kitchen
Contract manufacturer benefits from zero-shot learning
Contract manufacturers operate in a world where quality, speed, and adaptability are non-negotiable. With diverse product lines, demanding clients, and ever-changing specifications, maintaining high standards while maximising throughput is a daily challenge. Aicadium’s proprietary visual inspection technologies—template-based detection and pixel-level matching—offer a powerful answer.
The Challenge
Imagine a mid-sized contract manufacturer that produces millions of electronic assemblies annually for automotive, medical, and industrial clients. Their legacy manual inspection process was plagued by:
- Missed defects (20–30% undetected)
- Inconsistencies between inspectors and shifts
- Bottlenecks slowing production
- Rising labor costs and inspector fatigue
- Increasing product complexity and shrinking component sizes
With customer expectations and regulatory scrutiny at an all-time high, the manufacturer needed a solution that could keep pace with both volume and quality demands.
The solution
Now imagine Aicadium’s advanced AI solutions were deployed at critical inspection points across the production line:
Template-Based Detection: Cameras capture images of each assembly as it moves down the line. These images are compared in real time to golden samples of defect-free products. No retraining is required—when a new product variant is introduced, a reference image is uploaded and inspection begins immediately.
Pixel-Level Matching: For detailed verification, the system establishes pixel-level correspondence between each product and its reference. This allows for the detection of minute defects, such as missing or misaligned components, soldering issues, or surface anomalies.
Real world impact
The system identifies a wide range of defects—component misalignment, missing parts, solder joint issues, polarity errors, and foreign material contamination. Even defects too subtle for fatigued inspectors are detected instantly.
Every product is inspected to the same standard, shift after shift.
Reduced time for each inspection eliminates bottlenecks and boosts overall capacity.
When the manufacturer uploads a new reference image, the system instantly adapts, requiring no lengthy retraining or data collection.
Analytics dashboards track defect rates, recurring issues, and process drift, providing actionable insights for continuous improvement.
Comprehensive documentation and traceability reassure customers that their quality requirements are being met.
The results
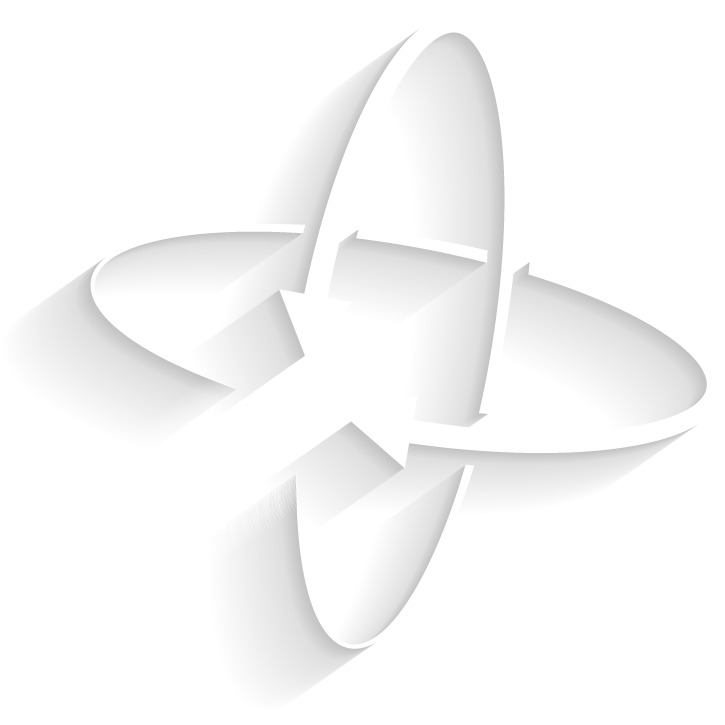
Aicadium View™ revolutionises inspection processes for manufacturing by transcending the limitations of traditional optical inspection methods.
Defect Detection Accuracy: Dramatic reduction in undetected defects, leading to fewer returns and warranty claims.
Operational Efficiency: Faster inspections and fewer bottlenecks enable higher throughput and lower labor costs.
Scalability: The system scales easily to new products and lines, supporting business growth without added complexity.
Competitive Advantage: The manufacturer’s reputation for quality and reliability is enhanced, attracting new clients and contracts.
By integrating Aicadium’s proprietary visual inspection technologies, this contract manufacturer could turn quality control from a bottleneck into a competitive differentiator—delivering better products, faster, with the confidence that only cutting-edge automation can provide.